CUTTING TOOLS
One of the Murphy's Laws about love states, "Love is the delusion that this one is different from all the others," but our proprietary recipe for carbide used in interrupted cuts really is substantially different from all the others.
Deep cryogenics is invaluable for all coated and uncoated cutting tools. The percentage of life expectancy increase depends on several underlying factors.
First and foremost is the heat treatment process itself. Inexpensive tools, purchased from industrial suppliers and known in the industry as bargain brands, are likely to have the worst content of retained austenite and show the greatest percentage of change. This is a great place to experiment to see what these tools will do before and after cryogenic treatment. It’s possible that these tools may outlast better grades of tools and reduce the initial out of pocket purchase cost.
A good example of this was using high cost T15 TiN coated premium drill bits to drill a very tight tolerance hole in an aircraft alloy. Fifteen holes could be drilled before losing tolerance. A very inexpensive, off the shelf, M3 drill bit wouldn’t produce one single good hole. After cryogenic treatment and resharpening to remove the thin film phenomenon, this low cost drill produced and unprecedented 200+ holes before it needed to be resharpened. The annual savings were estimated at over $100,000 per year for just one application!



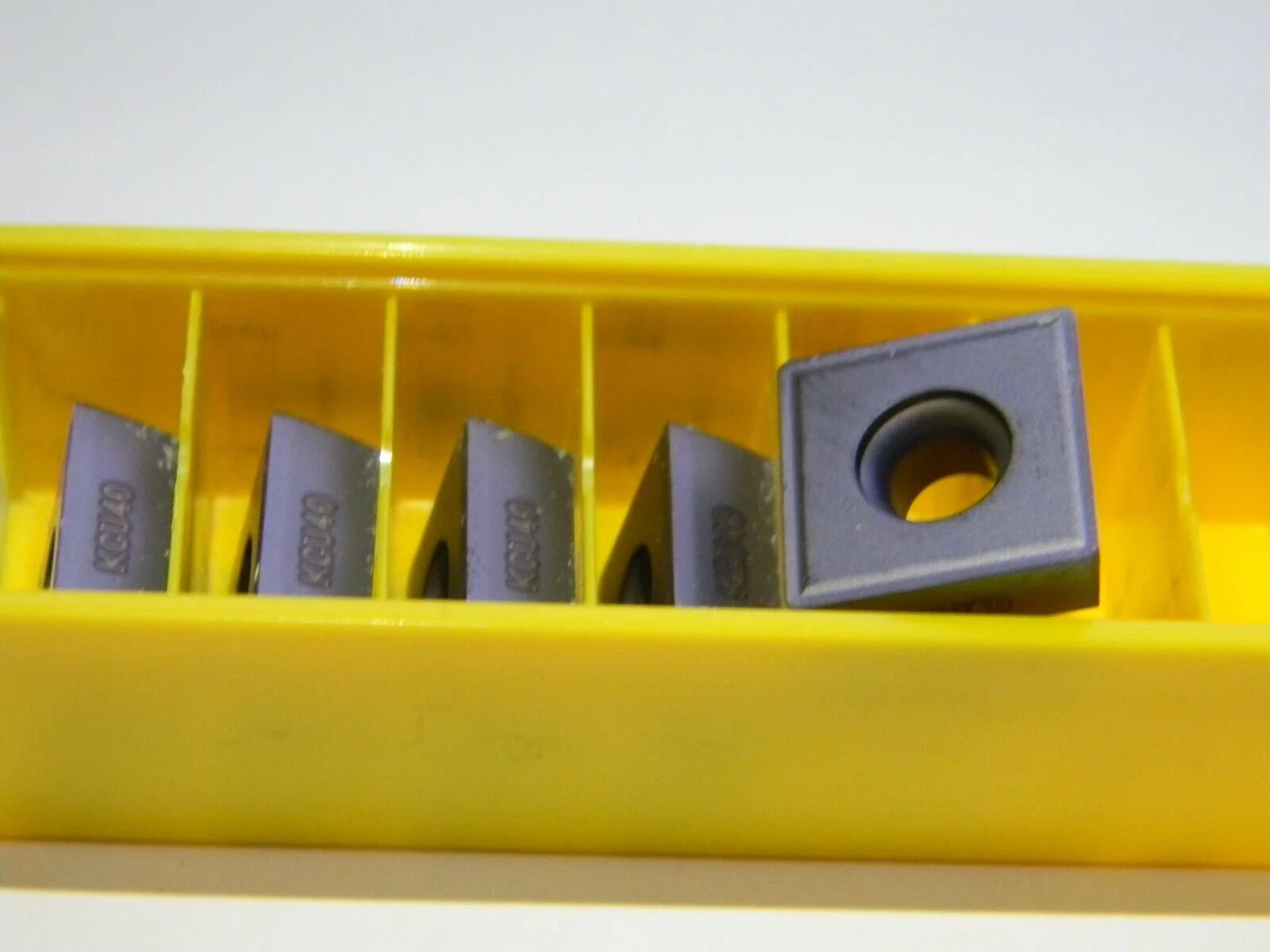
Carbide inserts and tools respond very well to the cryogenic process. In an Arizona State University study performed, they found “performance increases of up to 400%” to be realistic.
There is no austenite or martensite in carbide, so what makes the difference? The binder material that holds the grains in place is strengthened substantially. Most of the problem with the wear in carbide tools is the loss of the carbide grains on the cutting edge caused from the binder no adequately grasping the carbide.
In composition, carbide is like blacktop, where hard pieces of stone or slag are held together by tar. Carbide tooling consists of grains of carbide held together by a binder of cobalt, although some binder alloys are making it onto the market. In properties though, carbide is more like concrete. It is very durable, wear resistant, dimensionally stable and rigid. However, this rigidity causes it to be brittle and unable to withstand the impact and shock inherent to punching, milling, roughing and interrupted cuts.
The cryogenic process improves the holding strength of the binder material to keep the micro grained carbide in place. Cryogenics also acts as a stress relief from the high pressure sintering process under which carbide tools are created. Typically, carbides tend to at least double in life once cryogenically processed. How would you like to cut your carbide cost in half?
We have a customer who has a very consistent operation both milling and turning 1018 day in and day out. This enabled us to do some R & D which resulted in a recipe that consistently gives 2.3 times the normal life of Kennametal TiN coated carbide inserts when milling and four times the normal life of Sandvik TiN coated parting inserts on a CNC lathe. Our standard recipe had given no improvement in either case. Milling is an interrupted cut operation, whereas a parting insert is not doing an interrupted cut, but the tool design cannot help but result in vibration, which is a high speed shock that is beyond the ability of carbide tooling to withstand well unless it has been cryogenically processed with our recipe. The standard recipe we use for everything else gives four times the normal life of Sandvik inserts on the same CNC lathe turning the same material.
If you have a problem with carbide tooling in a milling or other interrupted cut situation, we would appreciate having the opportunity to help you. Try us and see. Our 100% guarantee is in place because we know our process works.
Cryogenic processing does not help reprocessed (recycled) carbide. Most carbide tool manufacturers add a certain percentage of recycled carbide to their recipe to reduce raw material costs. Therefore, improvement in wear life is brand dependent. We have never failed to at least double the life of Niagara or Sandvik carbide tooling.
Cryogenic processing does not help carbide tooling in an "abuse" situation. For example, we processed two carbide 3/8" drills, but produced no improvement. When we asked what they were used for, the shop foremen replied that they were drilling 62Rc shafts. They got two holes per drill and would have been happy to get three. Cryogenic processing can't help carbide in this situation. Another processor told us that he processed some eight ounce carbide inserts for a company that turns down railcar wheels. The wheels have voids in them and the inserts shatter when they hit a void. Carbide is unable to withstand such shock and cryogenic processing can't help in this situation, either. There are situations where this processing will not help, but our knowledge and experience can help uncover this and show the best solution to the problem. We are here to help!
CUTTING TOOL APPLICATIONS:
BAND SAW BLADES - BLANKING DIES - BRAKE DIES - CASTINGS - CHAIN SAW BLADES - CHIPPER KNIVES - CUT OFF KNIVES - CUTTING DIES - DRILLS - DIE CASTINGS - DIE SPRINGS - DIES - END MILLS - FORGINGS - FORM TOOLS - GEAR CUTTERS - GRANULATOR BLADES - GUILLOTINE BLADES - HOBS - PIERCING TOOLS - PLANER BLADES - PUNCHES - REAMERS - ROLL FORM TOOLS - ROUTER BITS - SAW BLADES - SLITTER KNIVES - SLOTTING CUTTERS - STAMPING DIES - STAMPING TOOLS - STEEL RULE DIE - TAPS - THREAD CHASERS